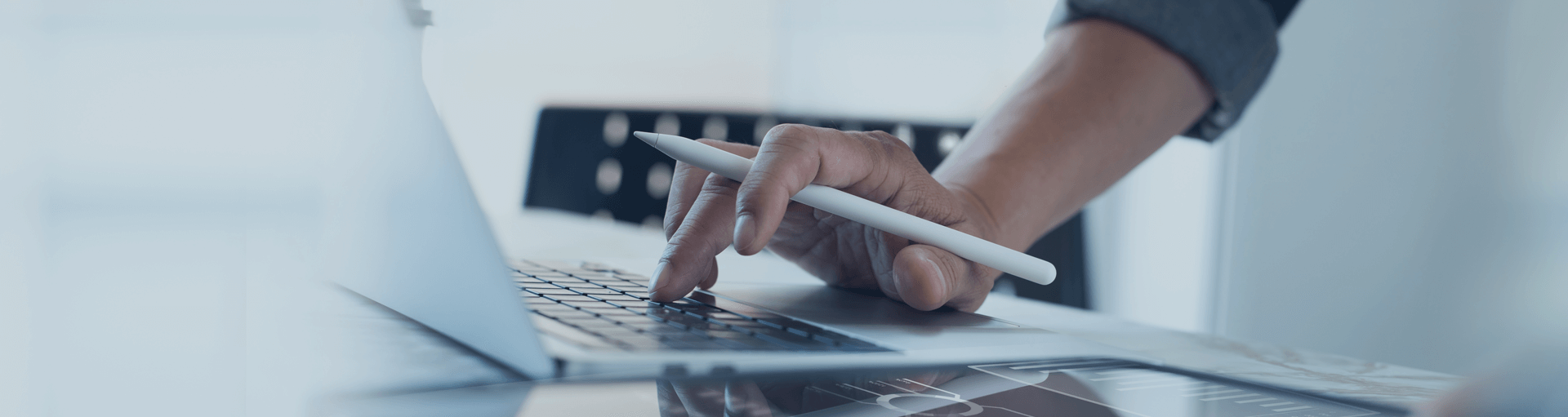
Blogs & Learning Center
Informative, thought-starting content focused on effective asset management
- All Topics
- Enalysis
- Detechtion
- Compressor
- Optimization
- Tech Tip
- E-Tip
- Monitoring
- reciprocating
- Enbase
- Maintenance
- Technology
- Thought of the Day
- Blowby
- Monitor
- recip
- Compression Management
- Key Performance Indicator
- webinar
- Field Operations
- EZ Ops
- Fieldlink
- Compliance
- Power Savings
- Representative Win
- Cost Savings
- Data Collection
- ESG
- Notification
- Screw
- failure prevention
- Capacity
- Case Study
- Control
- Emissions Reduction
- Enalysis 5.0
- Gauge Maintenance
- Logistics
- MSAPR
- Remote
- Satellite
- Simulate
- Sustainability
- Volumetric Efficiency
- ai
- moc
- rod load
- safety
- AER
- Articles
- Battery
- Callout
- Enbase Asset Monitor
- Mobility
- Remote Monitoring
- Upstream
- Usability
- Valves
- Vibration
- horsepower
Sort by
- Sort by
- Latest
- Oldest
- Read Time
Want to get the latest news and insights?
If you're interested in learning more, or would like to contribute to our blog, we'd love to hear from you. Contact us and let's collaborate!
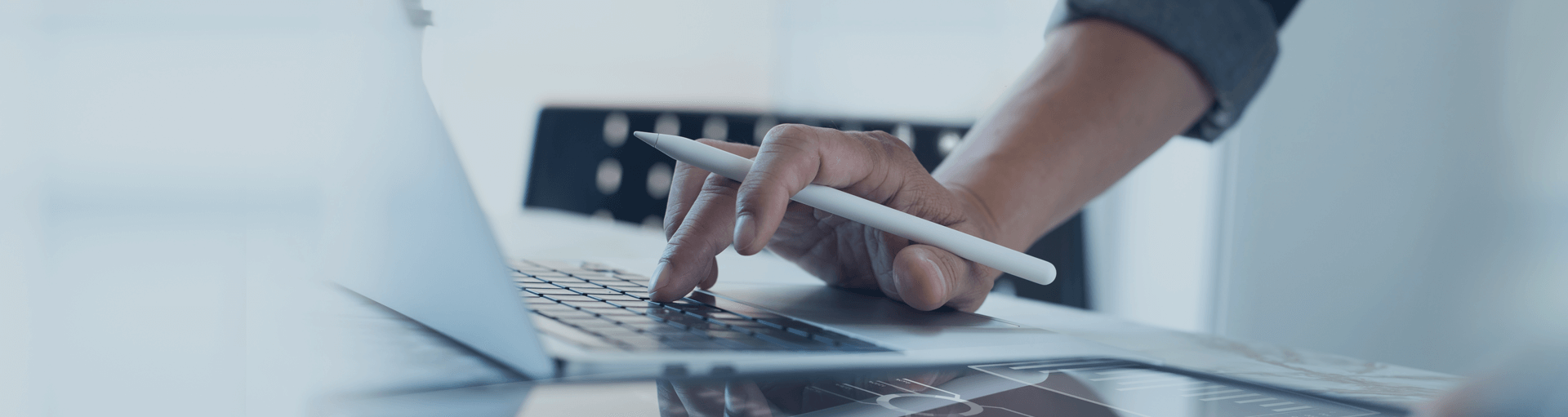
Want to get the latest news and insights?
If you're interested in learning more, or would like to contribute to our blog, we'd love to hear from you. Contact us and let's collaborate!
Seeing is Believing.
The BEST way to experience Detechtion is to see it for yourself. Schedule a demo and our experts will take you through how you can optimize your assets.