Houston, TX |
Unfortunately, there is a common misconception that if your gas rate is declining and your compressor is underutilized, there is no need to optimize it. Let’s explore a few reasons why this is not true.
The first scenario we will look at is a unit that is actively bypassing. The bypass valve works by stealing gas away from the high-pressure discharge side of the compressor (or from interstage) and rerouting it back to the suction line, helping to maintain an elevated suction pressure. Ultimately this means that you are compressing more gas than you are selling. Sometimes the bypass valve is opened during periods of start up to help warm up the equipment or to slowly introduce gas to the compressor, but if the bypass valve is constantly open, it’s likely that your Detechtion engineer will contact you about optimizing your compressor for your expected field conditions. The Enalysis report will estimate a theoretical, calculated flow based on your operating conditions that you can compare to your reported, or sales meter, flow. If these values don't match, the report will notify you that it suspects the bypass valve is open.
Let’s look at an example. The following compressor is operating at 1300 RPM, with all volumetric clearance pockets closed, from 20 psig suction to 1200 psig discharge, sending 3 mmscf/d from the field to the sales line. With this configuration, this compressor can move 4 mmscf/d at 20 psig suction. Since the compressor is configured to move 1 mmscf/d more than the field can deliver at 20 psig suction, the bypass valve is open.
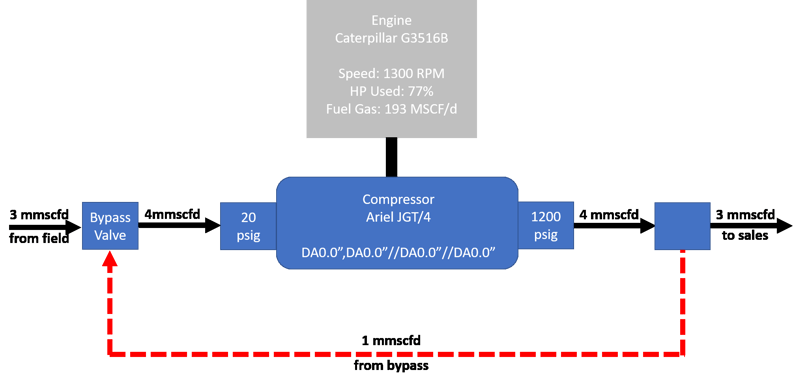
Generally, there are three things we can change about a configuration that would reduce the capacity of the unit which will help save fuel gas and horsepower so that the compressor only compresses as much gas as it is selling. Those three things are:
1. Lowering the running speed
2. Opening clearance pockets
3. Changing the configuration of the cylinder(s) from double-acting to single-acting
For this scenario specifically, we can achieve our target flow by both lowering the running speed and opening clearance pockets. As you can see from the table below, when we lower the running speed to 1050 RPM and open the first stage pockets a quarter inch each, the compressor is now only configured to move 3 mmscf/d at 20 psig suction. We can now operate this unit with the bypass valve closed. This compressor was not near max horsepower, and yet it still benefits from optimization with the help of Enalysis and a Detechtion engineer.

The next scenario we will discuss is optimization of multiple units by consolidation. In this example, the following 3 units are operating in parallel, compressing about 25 mmscfd of gas total from 115 psig suction to 1170 psig discharge.
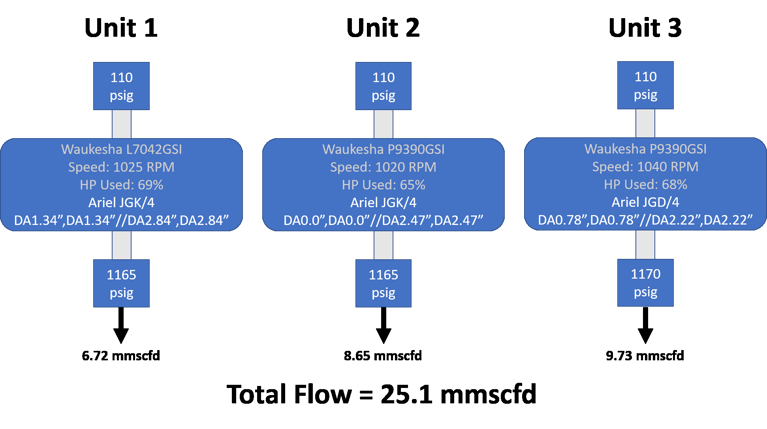
None of these 3 units are operating at or near max load. They are all operating between 65-70% HP with their bypass valves open. Let’s see if we can shut down one unit and optimize the other two so that the two running units can move the 25 mmscfd of gas. If so, by shutting down one unit we can save on operating expenses or rental costs, or we can move the spare unit to another site that could use the extra horsepower.
Units 2 and 3 are rated to a higher horsepower than unit 1, so we will see if these two can handle all the gas we need to move.
Unit 2 can move 11.6 mmscfd by closing the stage 2 pockets, closing the bypass valve, and bumping up the speed to max RPM. Similarly, unit 3 can move 13.6 mmscfd if we close the pockets and the bypass valve and increase the speed to max RPM. This totals our goal of 25 mmscfd through these two units alone, without having to run Unit 1 at all.
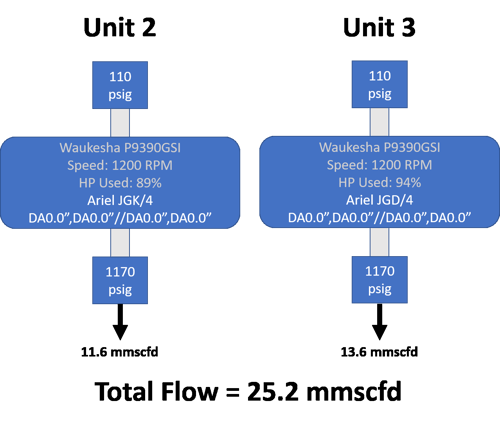
The tables below summarize the estimated annual savings in which this consolidation could result.

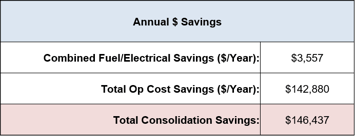
In addition to the two examples above, there are many other ways that a unit can benefit from optimization even when it isn’t at or near max load. For example:
- Single acting a cylinder instead of operating it with the volumetric clearance pocket fully open may help reduce valve wear rates due to low volumetric efficiency.
- Utilizing a volumetric clearance pocket to redistribute the compression ratio across a unit if you are dealing with high discharge temperatures on a particular stage could help to decrease valve wear or shutdowns.
Please feel free to reach out using the form below to learn more about how we can help you get the most out of your compression fleet or to let us know what challenges you are facing. We'll do everything we can to help you find a meaningful solution.