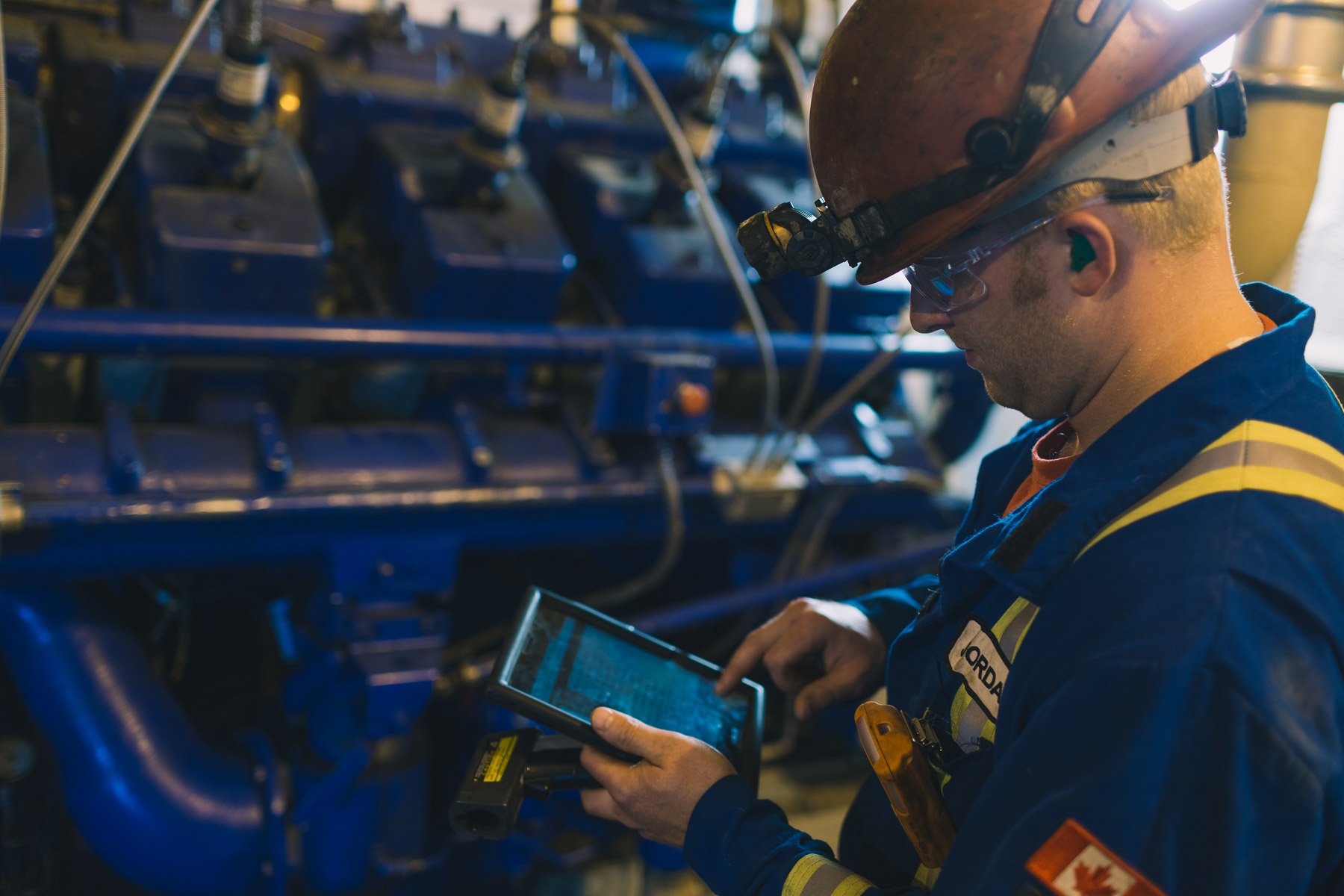
Optimize Your Chemical Management
Streamline Inventory, Delivery, and Compliance
Managing chemicals in the oilfield doesn’t have to be complex. Chemical Management solutions by Detechtion gives you complete visibility into inventory, simplifies vendor coordination, and ensures seamless compliance—empowering your team to reduce costs, eliminate inefficiencies, and focus on production-critical tasks.
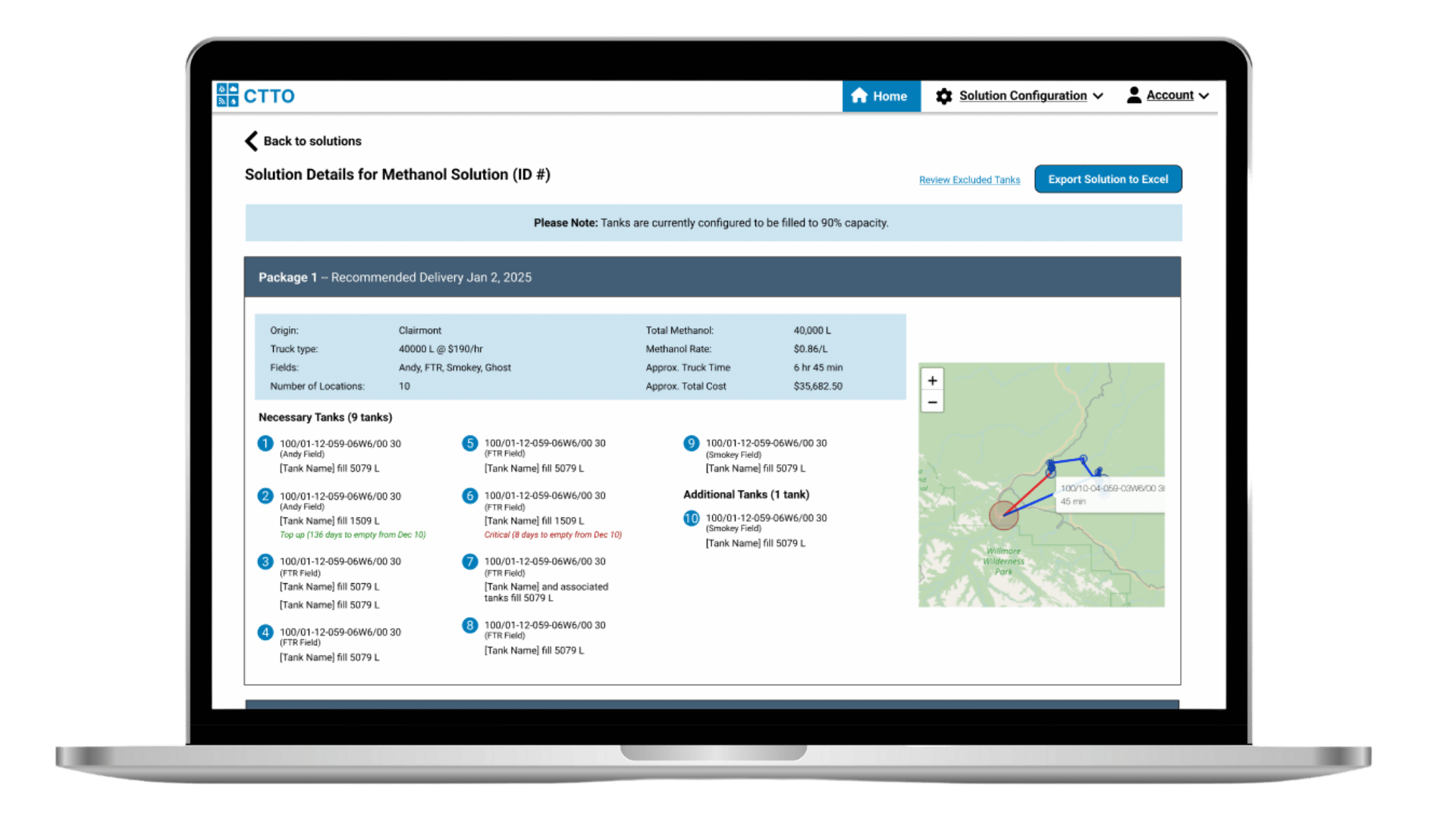
Take Control of Chemical Operations with Smarter Tools
How do oilfield teams navigate the complexity of chemical management, from inventory tracking to regulatory compliance?
Detechtion offers a purpose-built platform that centralizes chemical usage, automates workflows, and improves collaboration—ensuring operations run smoothly while meeting regulatory standards.
Core Capabilities Driving your Success
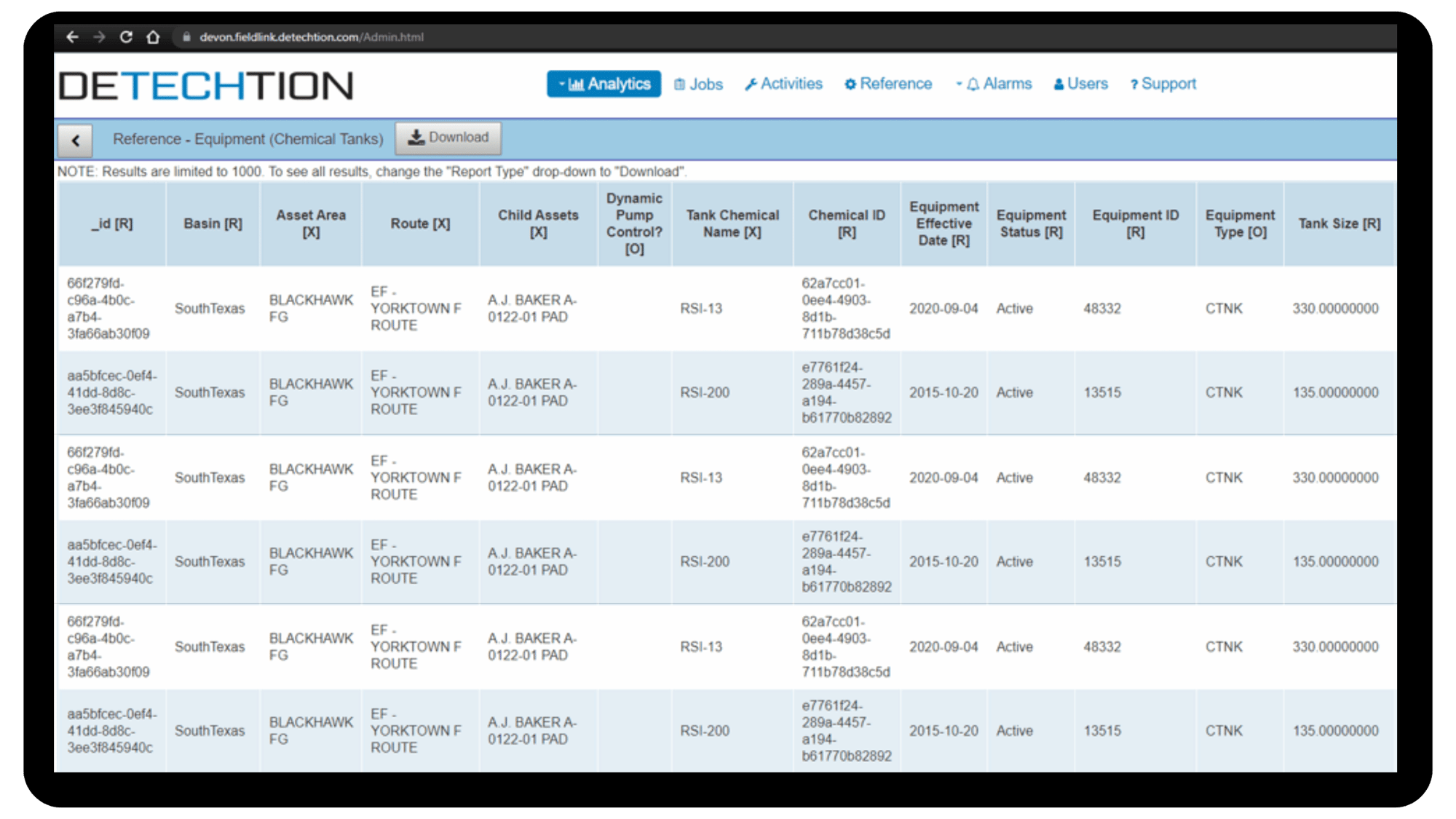
Provides accurate, up-to-date visibility into chemical levels across all sites, preventing costly shortages or overstocking.
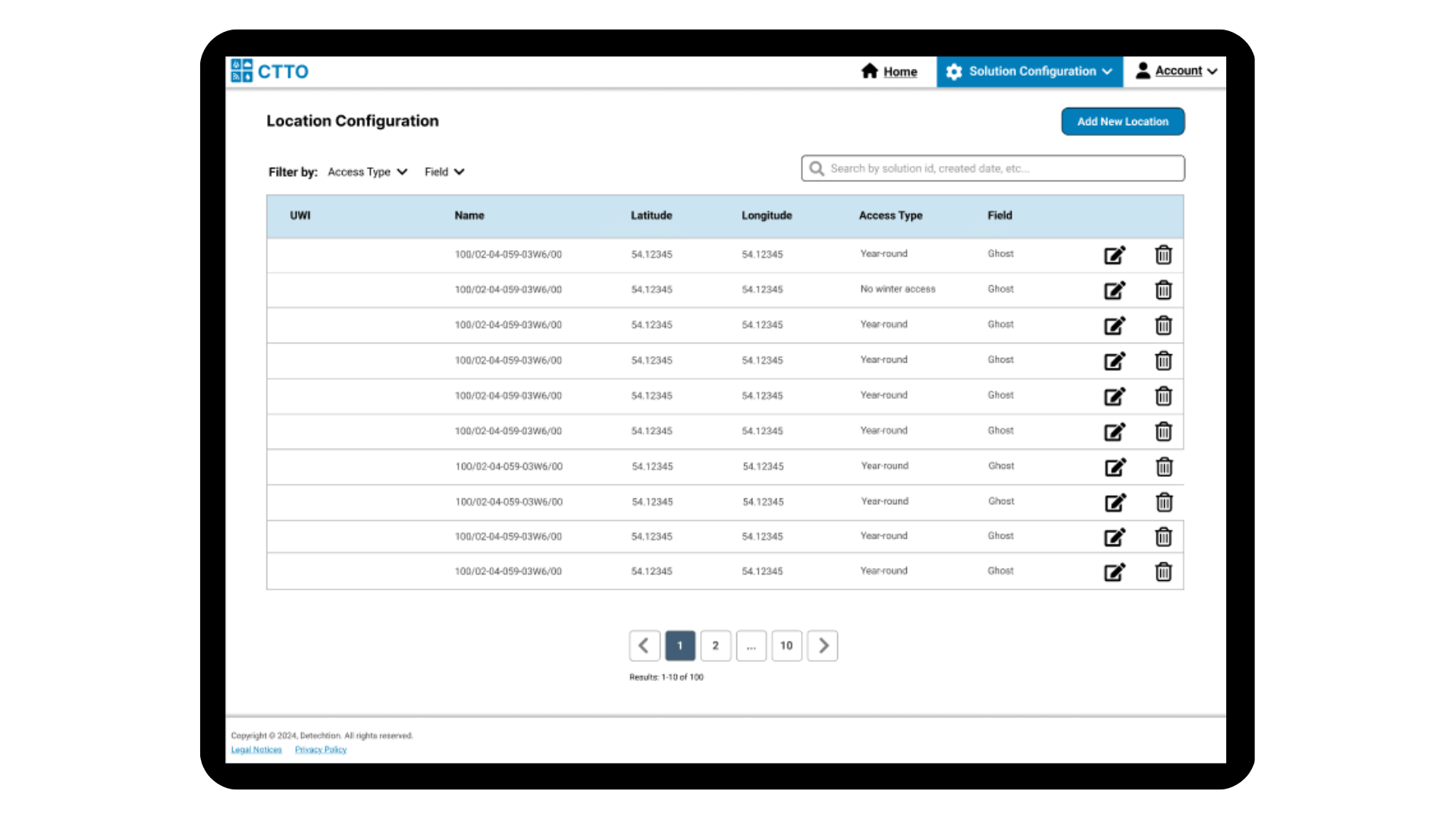
AI-guided route optimization ensures timely deliveries and minimized transport costs.
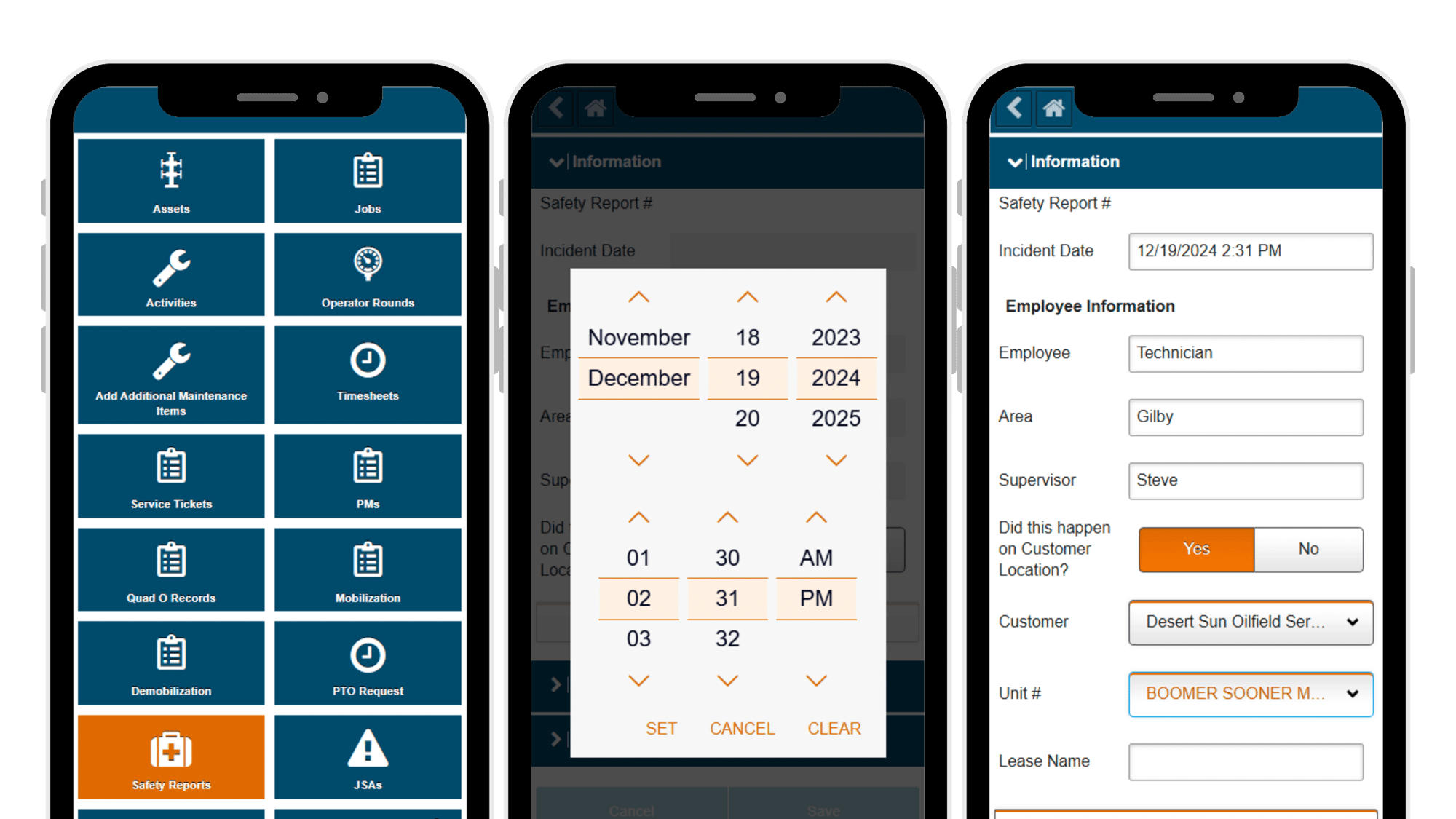
Tracks chemical usage, generates reports, and ensures adherence to regulatory standards, including EPA, OSHA, CEPA, and TDG Act requirements.
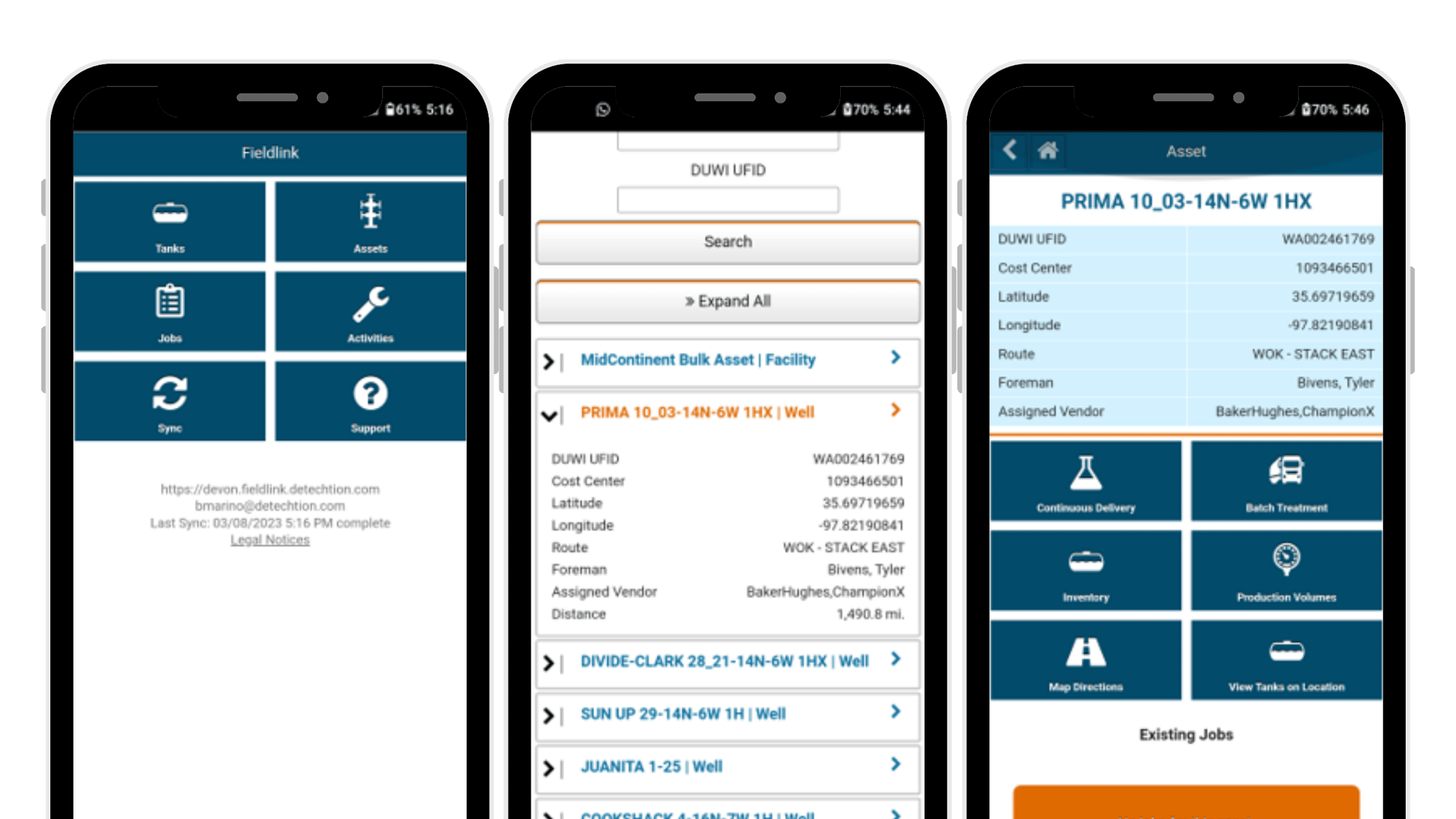
Centralizes chemical inventory, delivery schedules, and regulatory documentation in a single platform, eliminating fragmented systems and manual errors.
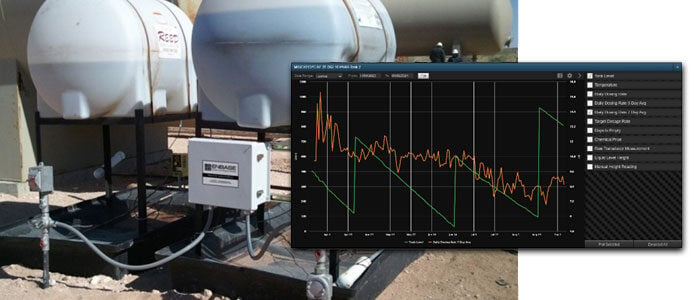
Enterprise grade integration allows for seamless connection to your existing infrastructure to ensure near real time visibility to flow meters, tanks, or chemical injection systems already in use.
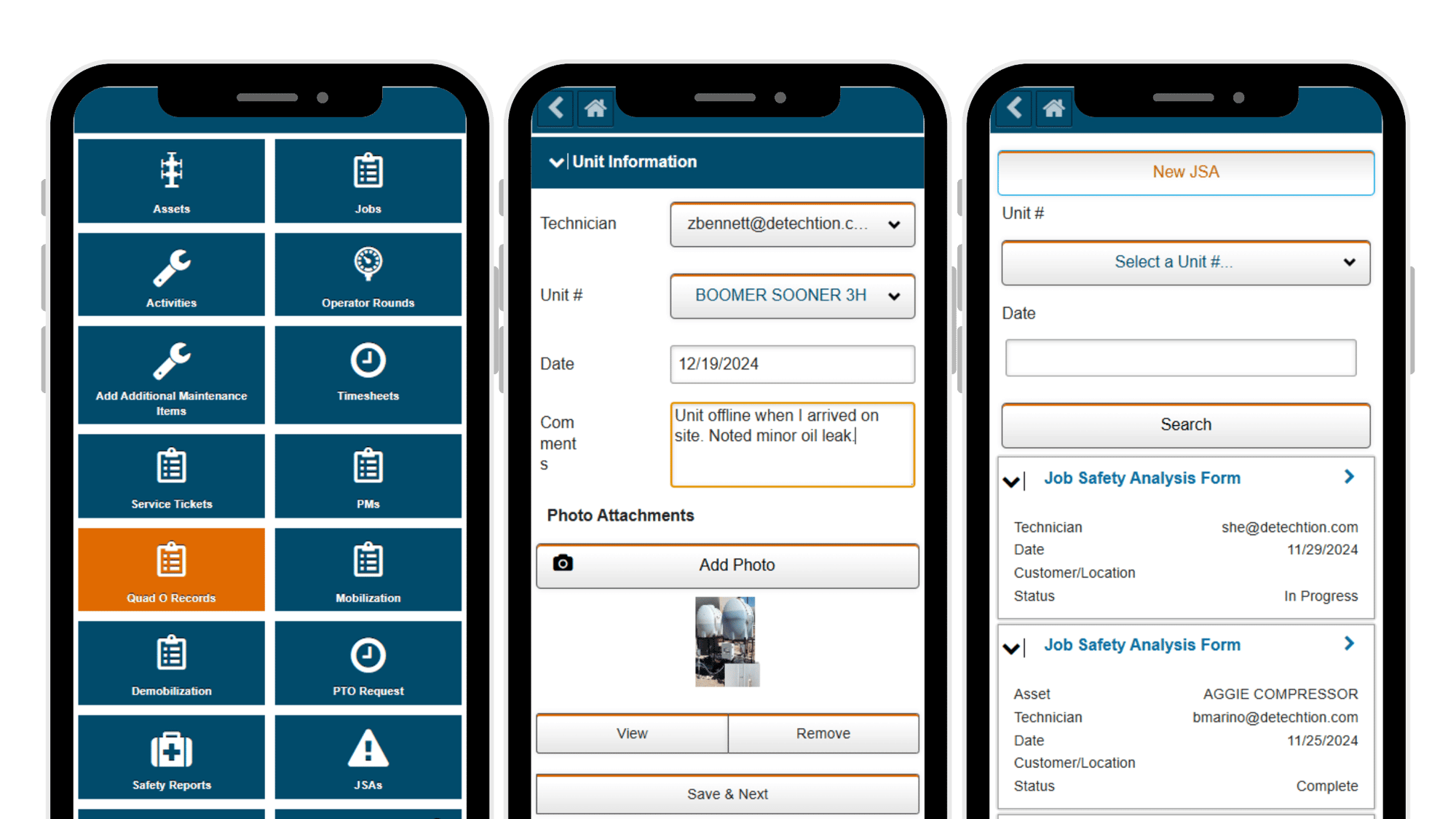
Adapts to your operation's unique needs with tailored workflows and robust reporting tools, ensuring actionable insights and smarter decisions.
Core Capabilities Driving your Success
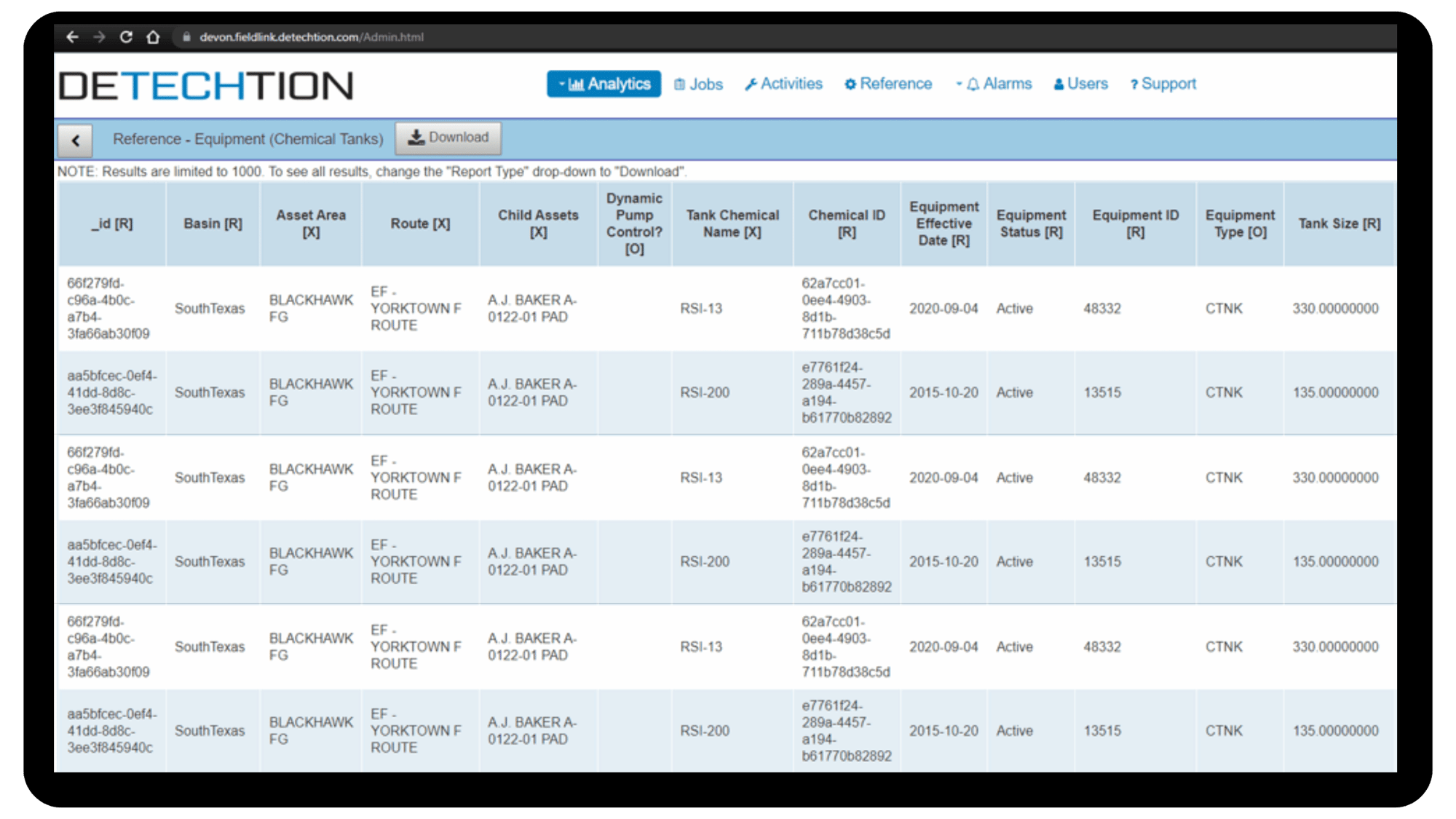
Provides accurate, up-to-date visibility into chemical levels across all sites, preventing costly shortages or overstocking.
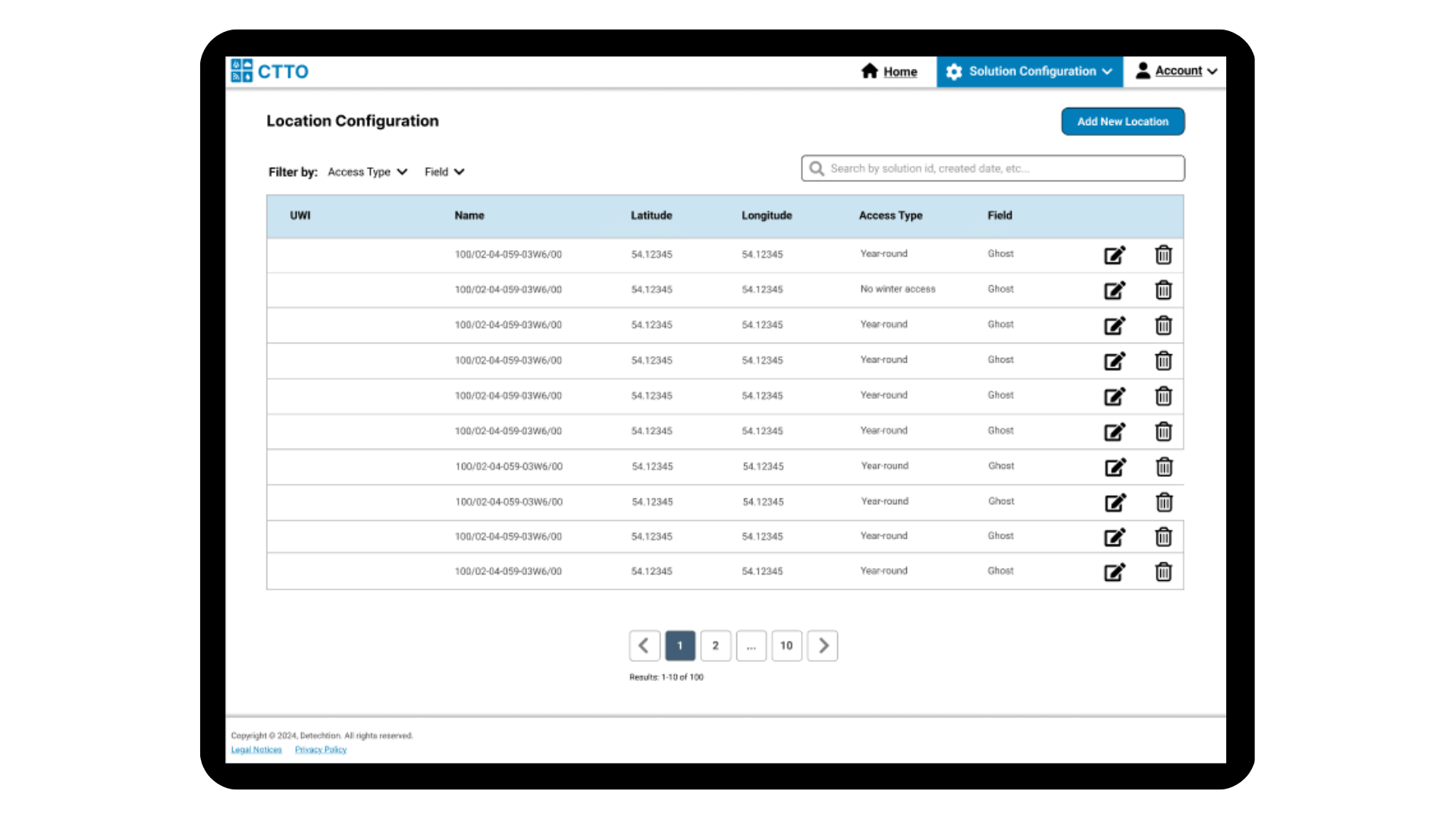
AI-guided route optimization ensures timely deliveries and minimized transport costs.
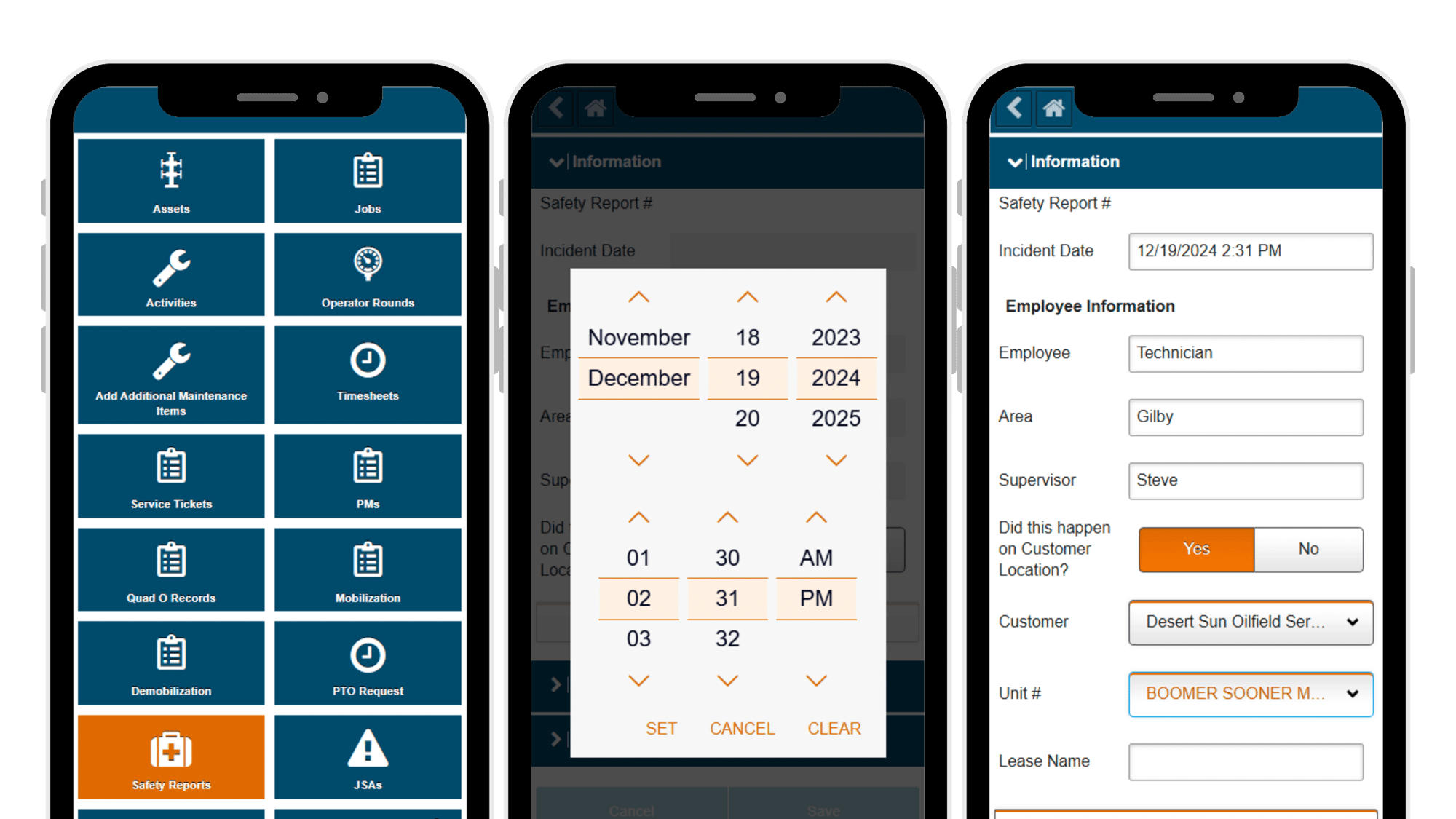
Tracks chemical usage, generates reports, and ensures adherence to regulatory standards, including EPA, OSHA, CEPA, and TDG Act requirements.
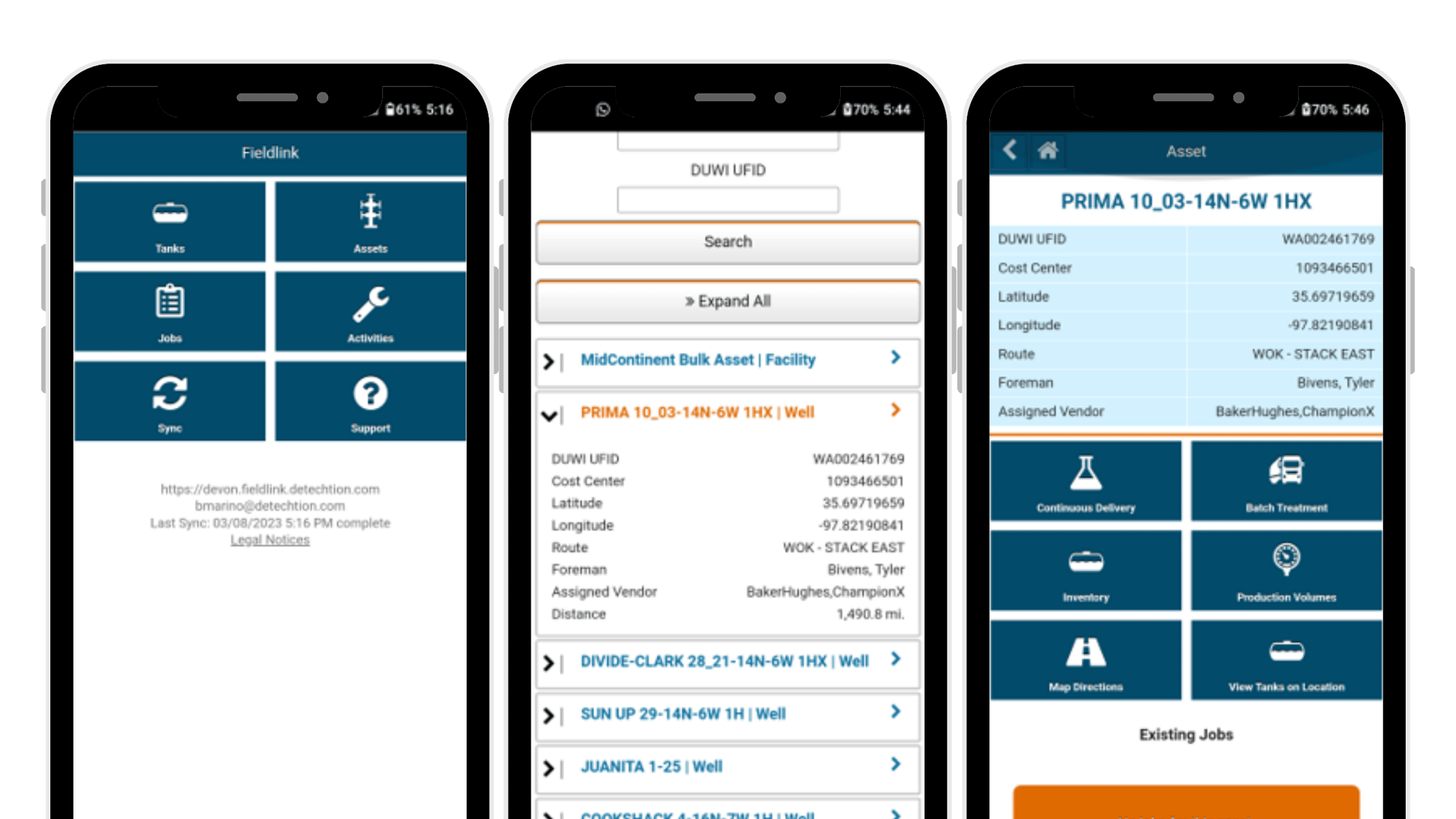
Centralizes chemical inventory, delivery schedules, and regulatory documentation in a single platform, eliminating fragmented systems and manual errors.
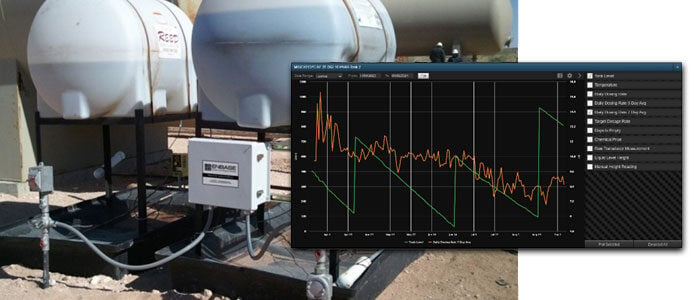
Enterprise grade integration allows for seamless connection to your existing infrastructure to ensure near real time visibility to flow meters, tanks, or chemical injection systems already in use.
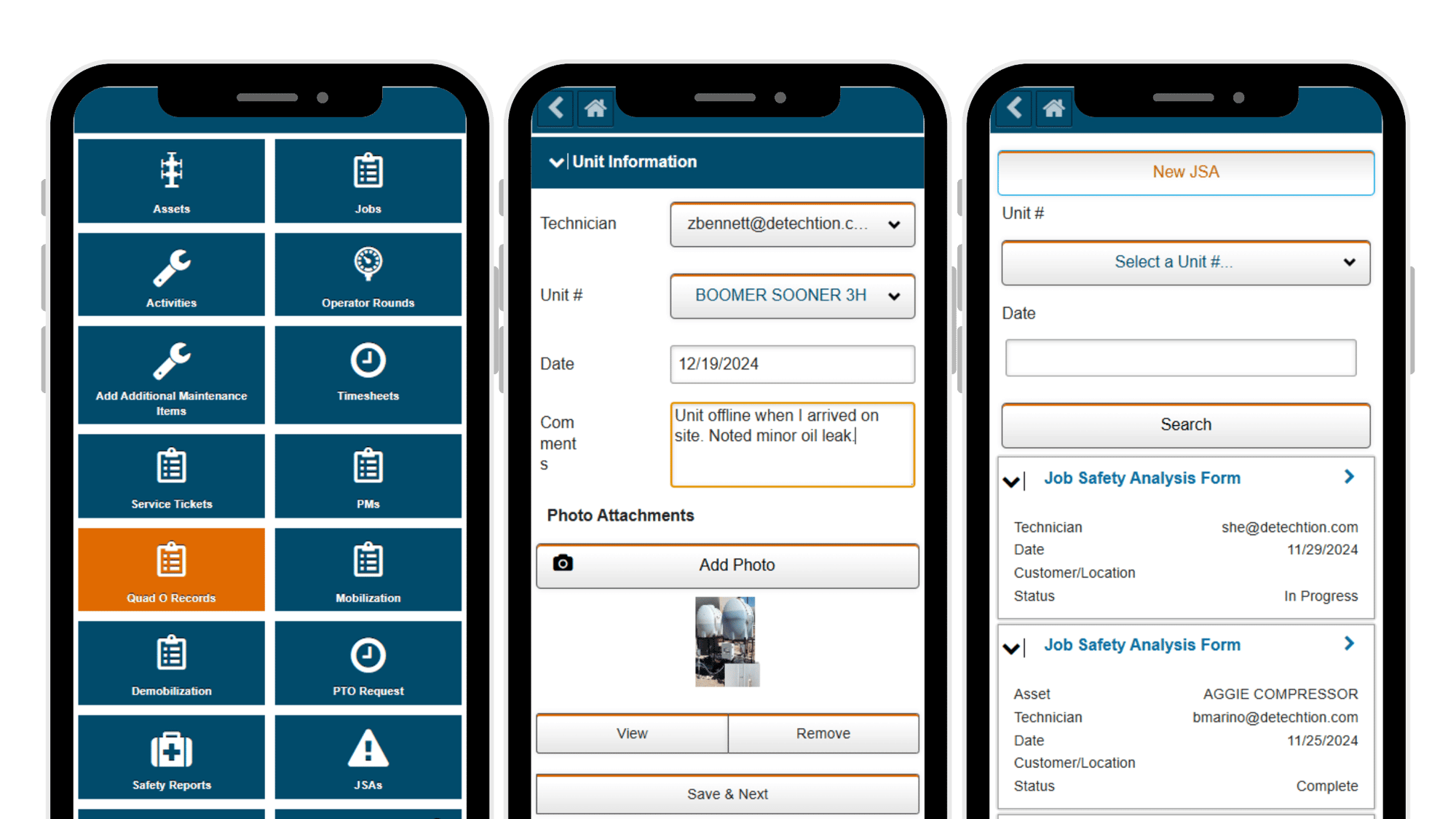
Adapts to your operation's unique needs with tailored workflows and robust reporting tools, ensuring actionable insights and smarter decisions.
Optimize Chemical Usage, Minimize Waste, Maximize ROI
Our clients experience measurable benefits by using Detechtion’s mobile-first Chemical Management platform:
Reduction
Better Load Utilization
Simplify and Optimize Chemical Operations
Key capabilities that transform how you manage chemical usage, inventory, and compliance.
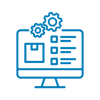
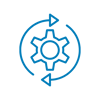
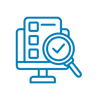
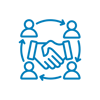
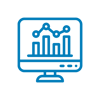
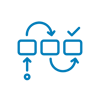
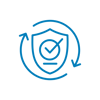
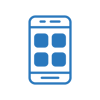
Protect Your People, Your Profit, and the Planet
We deliver end-to-end monitoring, control, and reporting solutions for chemical tank data, simplifying chemical management. Our solutions reduce costs and environmental impact all while optimizing oilfield production, data accuracy, operational efficiency and dosage safety.
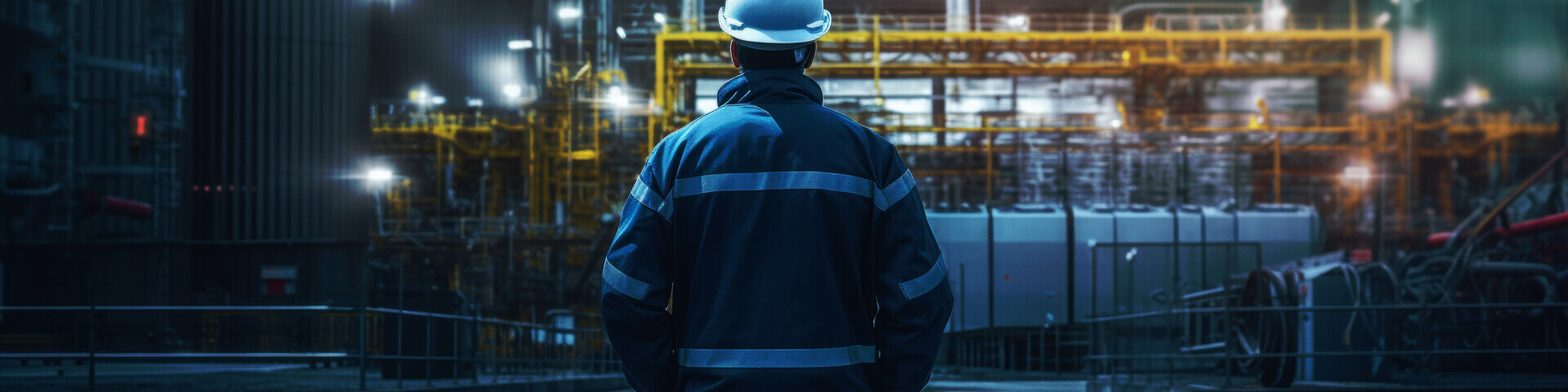
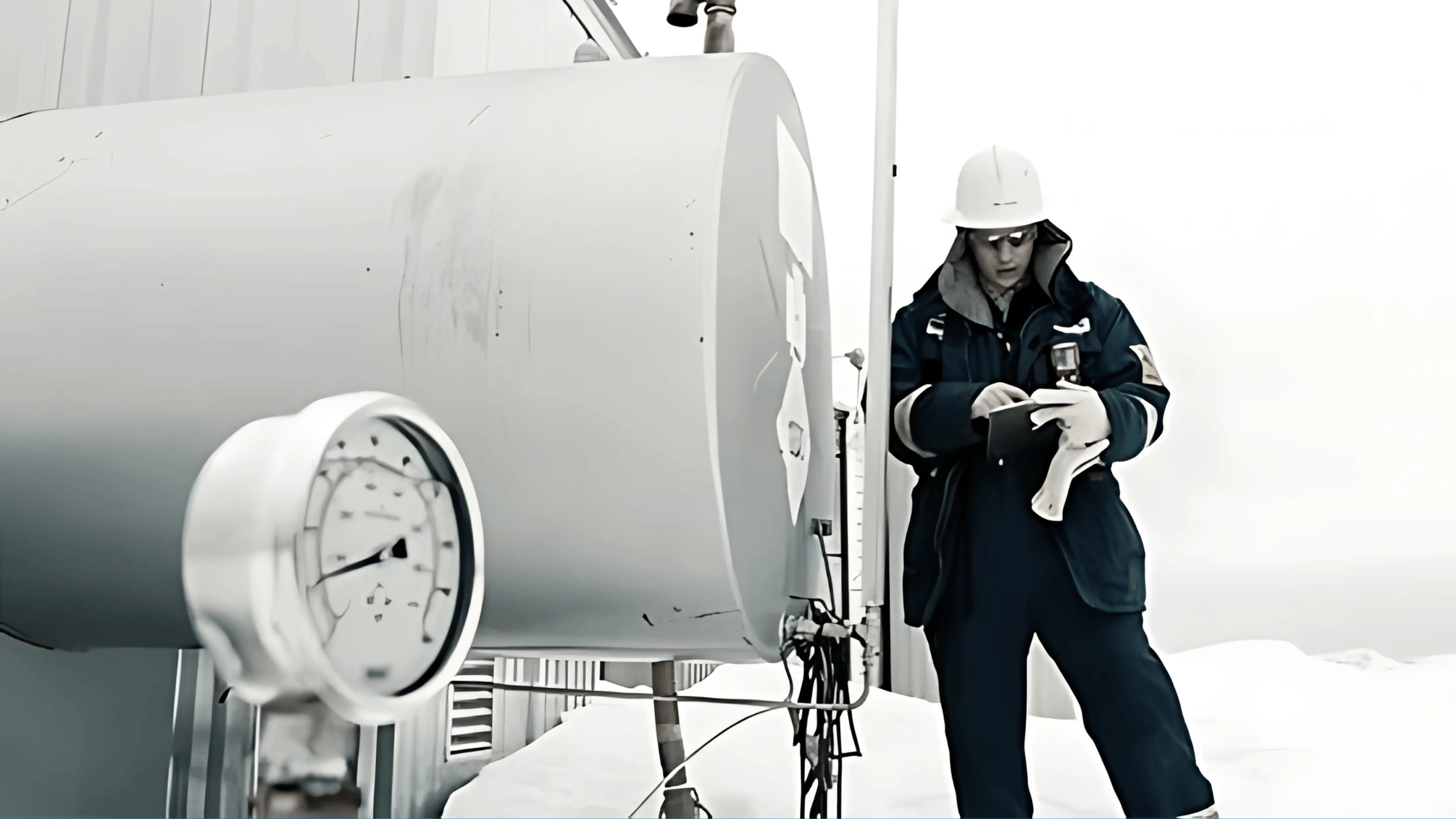
“Operationally, we didn’t experience the usual panic calls from operators worried about running out of methanol and freezing their pads.
This year, I haven’t heard a single call about methanol shortages, which is a clear win compared to previous years. While it’s hard to put a specific cost on it, every frozen pad involves significant expenses to restore. So far this fall, it’s been a big improvement..”
Logistics Operations Lead
at Major Canadian Producer
FAQs
When you decide to invest in a powerful piece of technology, no matter how user-friendly it may be, you’re still bound to have questions. We’re happy to help you as you discover the capabilities of Detechtion and are here for you every step of the way.
How does the platform help prevent chemical shortages or overstocking?
The solution provides real-time visibility into inventory levels, alerts for low stock, and actionable insights to optimize purchasing and usage.
Can the platform help with compliance reporting?
Yes, it automates the tracking of chemical usage and generates audit-ready reports to meet regulatory standards such as EPA, OSHA, and CEPA requirements.
Does Detechtion integrate with our existing systems?
Yes. The platform connects via APIs typically to existing SCADA, SAP, and IIoT devices to provide a unified view of your chemical operations.
Is the platform mobile-friendly for field operators?
Yes, it’s mobile-first and offline-ready, allowing teams to access and update chemical data from anywhere, even in remote areas without connectivity.
Explore our other Mobile Oilfield Management Solutions
Simplify Chemical Management Today
Ready to take control of your chemical program? With real-time insights, seamless compliance, and tools designed for oilfield teams, Detechtion powers chemical management that drives production and cuts costs.
.jpg?width=2000&name=Tanker%20with%20no%20logo%20(1).jpg)
Simplify Chemical Management Today
Ready to take control of your chemical program? With real-time insights, seamless compliance, and tools designed for oilfield teams, Detechtion powers chemical management that drives production and cuts costs.
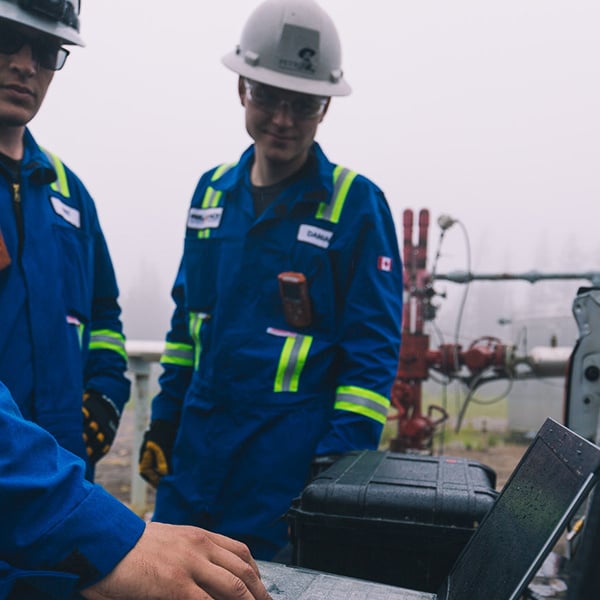
Natural Gas Company Reduced Opex by 18%
Read how one of our customers drastically improved their operations with our mobile solutions.
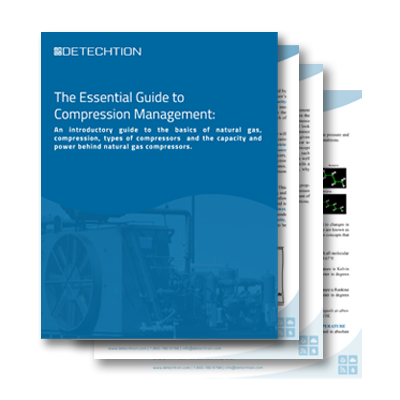
Compression 101
An introductory guide to the basics of natural gas, compression, types of compressors and the capacity and power behind natural gas compressors.
Welcome to the Future of Oilfield Efficiency
The next era of oilfield management is built on the foundation of accuracy, efficiency, and operator confidence. As an oilfield operator, you’re at the forefront of your organization’s evolution.
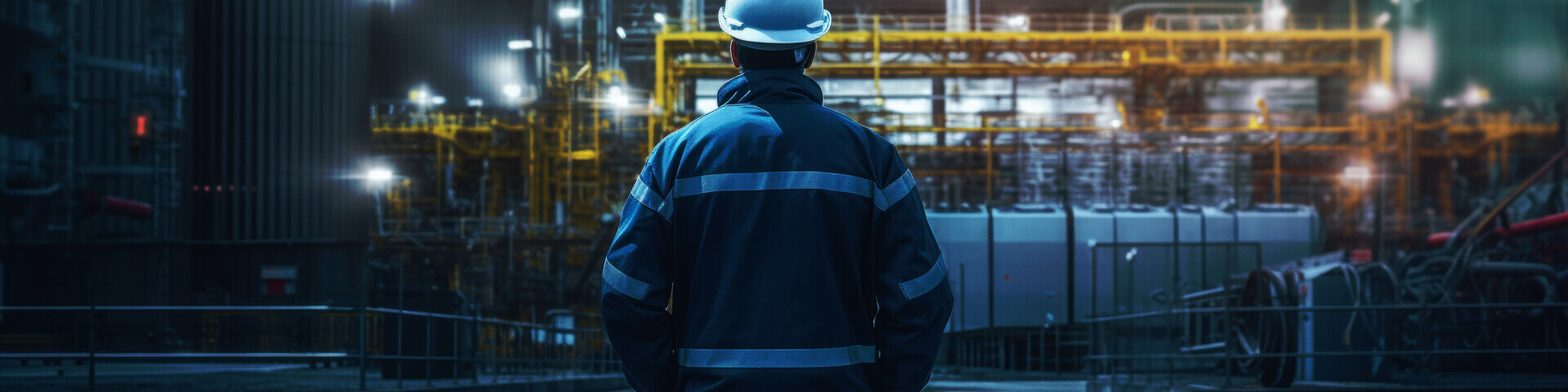